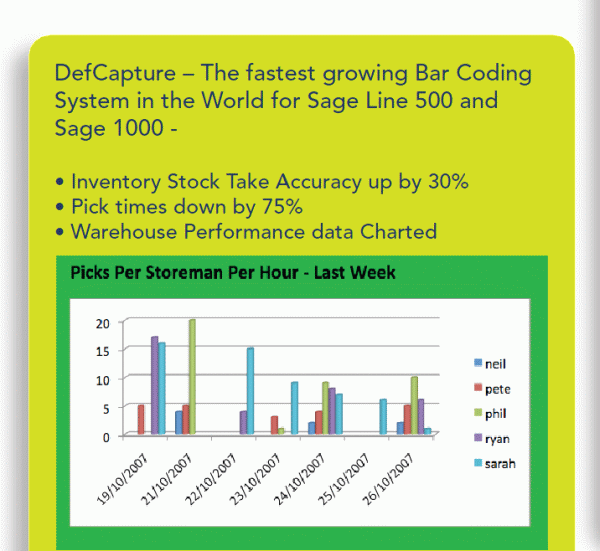
Call Us: +44 (0) 114 255 8599
Postcode: S8 0RX
Job Start-Stop Tracking – Increase visibility of shop-floor progress with bar coded real-time transactions Capturing accurate shop-floor operation times is paramount to manufacturing performance measurement. With detailed analysis of real manufacturing timings, variance against plan data can be determined allowing the rescheduling of work and the subsequent step-wise refinement of the process.
| ![]() |
![]() | Sage 1000 and Sage Line 500 provide a Work In Progress module which forms the corner stone for the tracking and analysis of manufacturing process data. The standard Sage module records after-the-event data such as how long an operation took and who performed the work.
The Defacto WIP Start-Stop module builds upon the Sage foundation module and offers an alternative approach. Instead of recording work completed, the module enables operators to clock-on to an operation and subsequently to clock-off. This also leads to increased visibility of progress, earlier alerting to problems, simplification of job time recording.
|
The Defacto WiP Start-Stop module offers an extension of Sage MRP II software into the shop floor and on to portable hand-held terminals. | |
Work-In-Progress Operation Time Tracking Using simplified entry points, jobs can be started by keying or scanning works order documentation and operator id. Job completion includes completed and rejected quantities. The data is collected and returned to the Sage production modules. | |
![]() | Work-In-Progress Inventory Tracking
By combining this module with the Defacto DefCapture module and on-line readers or portable readers it is possible to scan bar coded routing sheets to record part issues and assembly or sub-assembly completions as well as operation start and stop times. This solution can therefore report yield data so that work-in-progress costs and progress can be completely tracked. All data is immediately available with the Sage host system and can be viewed and monitored. |
![]() | The reporting is supplemented by new dashboard controls which can be embedded into Sage 1000 solutions or accessed independently in the Sage Line 500 environment. |
The dashboard typically shows Recent Operations Started and Completed, Recent Operation Rejects with reason and Reject Reason Trend. The Operations Completed within Standard Time chart can provide trend information including Variation.
Machine down-time such as breakdown or maintenance can be also recorded in start and stop time manner. Machine fault and events can be posted directly from the Defacto Planned Maintenance module. Likewise details of Operator start and stop times for events such as sickness and training can be recorded. For environments where routing information is standard and simple, the automatic routing feature of the module means that a standard route can be utilized throughout the system. For more complex routing scenarios, the module fully integrates with the standard Sage WIP and Routing. 2009 versions of this module also provide auto-book on and set-up time postings as well as faster links to machine down time entry. The 2010 versions of this module now also support full time sheet entry for faster posting of WIP Tracking information. The module integrates with the standard Sage Works Order Processing modules to provide summary times and costs, visible at works order header and operation level. Defacto Universal Interface module now supports WIP postsings compatible with this module.
| ![]() |
The dashboard detail is pre-release draft information. The dashboard is currently in alpha test. Some features may vary from the descriptions above.
These products require Microsoft Internet Information Server and Sage 1000 or Sage Line 500 running the Defacto Universal Interface module on a Windows .NET 2.0 platform.
Installation of the standard WIP and Routing modules is optional, but is required if detailed Routes are needed.
Installation of the standard WIP is optional, but provides additional WIP tracking capabilities and enquires.
Web Services for Sage – Universal XML and SOAP Interfaces to execute Sage 1000 Transactions
Defacto WeboB provides a web service interface to Sage 1000 and Sage Line 500 allowing external parties to create sales orders, purchase orders and works orders along with reference data such as Inventory items, Customers, Suppliers, Services in the Distribution and Finance modules and Bills of Materials and Routes in the Manufacturing modules.
| ![]() |
The package delivers a means of exposing key Sage functionality to third party developers and system integrators, hiding the complex Sage business rules through a simple interface while at the same time protecting the Sage database.
Defacto WeboB also provides services to execute a wide range of transactions within the Sage environment. The initial release supports inventory transactions including sales order despatch and purchase order receipt, as well as stock take and ad hoc adjustments, bin to bin and inter-warehouse movements. Support is also available for the manufacturing environment for Works Order Issue and Completion, and WIP Tracking including Stop-Start postings through the Defacto WIP Stop-Start module.
![]() | |
The Defacto WeboB includes a set of W3C Web Services which can be installed on the enterprise server within the intranet or on an external web server which means the module can be used to connect homogeneous businesses together at departmental and enterprise level as well as offering an alternative to conventional EDI for co-operating businesses.
|
Supported by the proven technology of the Defacto Universal Interface module, Defacto WeboB provides a validated and safe interface to manipulate the Sage database from an external third party source.
CASE STUDIES
Defacto WeboB can be used as a component in building linked systems such as:
Web Sales Back-end – integrating a third party web-sales environment to directly create sales order or invoices within the Sage system to publish a sales portal on the WWW.
Inventory Carousel Interface – providing automatic updates to Sage inventory for put-away and retrieve transactions from warehouse systems reducing double keying.
Customer Returns Portal – creating a customer-facing interface to handle returns queries enhancing customer service performance.
Sub-Contractor Interface – importing and exporting material call-off and operation time and progress data to synchronize Sage production with off-site processing.
Basic Webob Services are available, more services are being added. This is pre-release draft information. The module is currently in alpha test. Some features may vary from the descriptions above.
These products require Microsoft Internet Information Server and Sage 1000 or Sage Line 500 running the Defacto Universal Interface module on a Windows .NET 2.0 platform.
For Web Services to be published on an external web server, it may be necessary for the organization to configure firewall settings to enable a route to the Sage database. All trade marks acknowledged.
DefCapture – Bar Coded Data Capture solutions for Sage 1000, Sage Line 500 and Sage X3
With today’s need for an agile supply chain, bar coded data capture can deliver improved speed and accuracy, decreasing employee time to process and overall transaction costs.
DefCapture from Defacto provides a flexible solution to bring bar coded data capture to the Sage 1000 and Sage Line 500 and Sage X3 environments
|
![]() |
Aimed at companies who want to enjoy the improved data entry efficiency possible with bar codes out of the box without the expenditure and effort of installing and integrating a non-Sage third-party warehouse management system, DefCapture offers a simple yet flexible front-end to the Sage installation.
Benefit from:
Goods receipts - purchase order shortages can be immediately determined and check on the spot, rather than after items have been partially moved. Critical parts can be routed to manufacturing immediately.
Put-Aways in real time – as soon as items are put away, they immediately become available for sale or for manufacturing.
Sales Order Picking - select from multiple modes of picking and packing management including fully guided picking where the system leads the operator to the correct pick locations and confirms correct item selection. More information on Picking modes.
Replenishments - keep pick faces ready with built-in shortage and replenishment management and overall warehouse husbandry.
Works Order Kitting and Completion - manage manufacturing processes using line side kitting, backflush, quality control and completion. Guide the operator to pick or assemble and verify as the operator scans each part or subassembly correct specifications.
WIP Tracking - machine and resource utilization recording for real time visible of production progress.
Stock Counting - Periodic and Perpertual Inventory solutions using Location Guidance based on Sage Stock Take Cards.
Kan Ban management – as soon as items are issued, the system can report back stock below re-order level, request a stock count and initiate replenishment actions.
Despatch confirmation – with the system leading the operator to the correct pick locations and confirming correct item selection, accurate consignments can be quickly assembled and verified.
![]() |
The DefCapture architecture makes it is possible to start with a single transaction type and add further transaction types and devices as opportunities for efficient data entry are identified. Starting with a single-scanner Goods Inward system a system can grow at the business’s own pace into a multi-scanner, multi-transaction suite supporting Production, WiP and Stock Taking. Alternatively a full and comprehensive end-to-end Warehouse Management System can be specified from the outset. In this scenarios, a DefCapture implementation still offers the option to introduce functionality step-by-step which reduces risk and allows for easier management of the project.
|
All options can easily be configured to provide pre-defined and terminology to it is possible quickly create a customized solution to match the business. For example a "Secure Cage Issue" option can be configured by pre-setting the location of the "Secure Cage" and changing the menu text to match the terms used in the business. Options can then be deployed and controlled on a per-user basis.
Hardware solutions can include mobile devices such as handheld scanners linked using the common wireless standards 802.11b/g for portable data capture in real-time, as well as fixed scanners, web clients and existing Sage PCs. Wireless Tablets offering large colour screens can be carried asminiature management dashboards. Established brand name devices such as the Zebra (Motorola) range can be utilized with the DefCapture. These devices included traditional guns as well as wearable terminales. Defacto demonstrated the use of an Apple iPad for Warehouse Picking and Management at a recent conference. Android devices may also be used. Defacto recommends Zebra wireless infrastructure and devices which yield the benefit of pre-emptive roaming and power management. We can arrange for our hardware specifical team to conduct a site survey to assess requirements.
|
|
![]() |
Underpinned by the proven technology of the Defacto Universal Interface module, DefCapture provides a validated and safe interface to manipulate the Sage database from an external third party source. Developers can therefore work in a "managed" environment producing solutions based on the Sage business objects exposed by the interface. System Integrators and IT Departments can also use the underlying .NET framework which the module delivers to extend and develop custom user interfaces on Windows CE and Windows Mobile devices to handle specific bar code entry requirements; the solution is flexible and extensible. |
DefCapture provides bar coded data entry of a wide range of transactions within the Sage environment. The solution can handle inventory transactions including sales picking and order despatch and purchase order receipt and put-away, as well as stock take and ad hoc adjustments, bin to bin and inter-warehouse movements. Support is also available for the manufacturing environment for Works Order Issue and Completion, and WIP Tracking including Stop-Start Postings through the Defacto WIP Stop-Start module.
|
|
![]() |
PhotoScribe recently demonstrated how to read a bar code that had been inscribed on the girdle of a diamond. |
The Defacto products are being continually developed and some features may vary from the descriptions above.
These products require Microsoft Internet Information Server and Sage 1000 or Sage Line 500 or running the Defacto Universal Interface module on a Windows .NET 2.0 platform. DefCaptureX3 is alos available for Sage X3 solutions.
An 802.11b/g wireless infrastructure is also required for hand-held device communication.
All trade marks acknowledged.